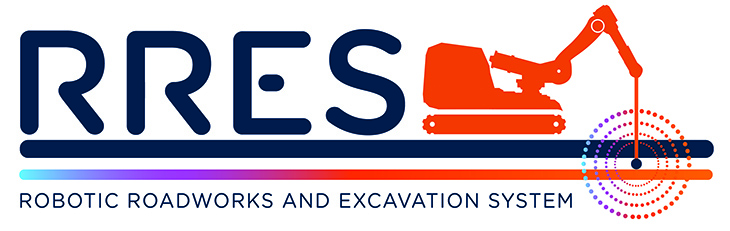
In 2018, we won our fourth Network Innovation Competition (NIC) with a bid to develop a Robotic Roadworks & Excavation System (RRES) which will improve existing methods of excavation, repair and maintenance operations performed daily at SGN and the other Gas Distribution Networks (GDN).
All utilities face an ongoing challenge in safely and efficiently managing excavation activities. This will continue for the life of the assets as they are pushed to return their maximum value for the GB customer.
RRES aims to reduce the required excavation size, labour costs, and equipment while making the work safer. The project will automate the excavation process in both rural (transmission) and urban (distribution) areas using artificial intelligence (AI) and advanced robots.
Why RRES
Utility excavations are necessary to inspect and maintain buried infrastructure, but are disruptive, labour-intensive and can lead to unintentional damage to neighbouring plant. Reducing the requirement for extensive safe digging practices could significantly reduce both the social cost of works and associated emissions.

RRES aims to address three main problems associated with utility excavations on both the Distribution and the transmission infrastructure:
- Operating Costs
Excavation for both distribution and transmission works require multiple teams from project start to completion. A single excavation represents a major investment of time, labour and money including field and office/support personnel, numerous vehicles, tools and equipment and all associated permit costs. Rural excavation is particularly costly due to the requirement to hand dig and the inclusion of extensive safety precautions, while operating near the transmission pipeline.
RRES looks to automate the excavation process, creating a much smaller excavation when compared to traditional methods. Costs will reduce as the operation will require less: traffic management, labour, material and lane rental charges.
- Disruption and CO2e
Utility excavations often require a large physical footprint to accommodate multiple vehicles, heavy equipment and numerous teams. These work sites can create a public nuisance by causing major disruption to traffic flow and obstructing access to local businesses and residences.
Compared to traditional excavation methods, RRES will have a much smaller physical and carbon footprint. Not only will this will reduce our carbon dioxide emission, but also reduce traffic and pedestrian delays to both business and public users of the highway.
- Excavation Damage
Historical mapping methods for electricity, water, sewer, communication and gas infrastructure along with limited locating technologies can lead to accidental impacts during excavation, causing service disruptions, serious damage, loss of property and sometimes fatalities. Cable strikes represent a real and serious hazard due to the risk of electrocution, fire or explosion.
RRES utilises the soft touch tool, coupled with the ability to sense buried utilities and objects. This will enable a redundant safety feature in the excavation operation which will improve safety to our operatives and stakeholders.
Technical information
The goal of the project is to develop and test a RRES prototype system that can demonstrate automation of the excavation and reinstatement process and the installation of a Universal Access Fitting (UAF).
The system fuses advanced robotic arm technology with a mobile platform and will be controlled by AI using a suite of sensors and feedback controls to enable autonomous, safe and efficient mains excavation.
Below-ground sensors
Before starting any excavation, RRES uses a host of different types of sensors to build a detailed and very accurate picture of the ground beneath it. The robot automatically scans the area and a computer algorithm then processes the data, combining it to create a map. RRES then generates a three-dimensional model of underground assets, enabling the team to plan a site for excavation with complete confidence.
Road cutting device
RRES is now equipped with a road cutting device to cut and remove a keyhole shape from the road surface. Unlike traditional methods, the device can cut any shape into the road. Using AI, the robotic cutting arm can sense material hardness and adjust the cutting speed, which extends the lifetime of the tool by automatically tailoring the use and strength needed.
Soft touch excavation
With the keyhole removed, the soil above the asset is excavated. RRES uses supersonic air nozzles to agitate the soil, which is then removed with a vacuum suction mechanism. The tool head has sensors to detect any asset that is close to the excavation site, allowing for further inspection and avoiding damage. The quantity of sensors allows RRES to create a three-dimensional understanding of what is around the operational area.
Backfill
The robotic arm is integrated with an air compactor for reinstatement of the loose material that was put aside from the excavation. Sensors measure the soil compaction level and soil is returned in layers, compacted to mirror the density of the surrounding subsoil. Finally, the road surface key is replaced and sealed.
Project benefits
The RRES project will yield potentially significant financial, safety, environmental and social benefits by combining modern automation and robotic technologies to solve a daily challenge in the utility and construction sectors. Benefits are cross transferable to a number of utility, infrastructure and construction sectors.
The benefits, learning, and improvements include:
- Smaller excavations will improve efficiency and reduce our carbon footprint, subsequently decreasing disruption to the public
- Operating costs will be reduced as operations will require less traffic management, lane rental charges and material
- By utilising the soft touch tool coupled with the ability to sense buried utilities and objects, it will enable a redundant safety feature in the excavation operation. This will improve safety to our operatives and stakeholders
- By removing the operatives from the immediate excavation area, the safety risk is lowered
- Open market for expanding future inspection, maintenance, and repair operations;
- Robotic automation of works will remove operator from immediate excavation site making it safer for operatives
Publications
You can find out more about our project below.
RRES Project Progress Report 1 - September 2018
RRES Project Progress Report 2 - December 2019
RRES Project Progress Report 3 - April 2019
RRES Project Progress Report 4 - August 2019
RRES Project Progress Report 5 - November 2019
RRES Project Progress Report 6 - March 2020
Working together
At SGN, we pride ourselves on our customer focus. Our philosophy of putting the customer first will be at the heart of this project.
If you want to discuss RRES and share your views, we want to hear from you. Contact us at any of the following:
Email: rres@sgn.co.uk
Write to: RRES team, SGN Axis House, 5 Lonehead Drive, Edinburgh, EH28 8TG